The function of the mold feed system is to make the high temperature melt under high pressure go into the mold cavity to fulfill that.
The style and quantity of gate and feed style often determine the specifications of plastic mold base.
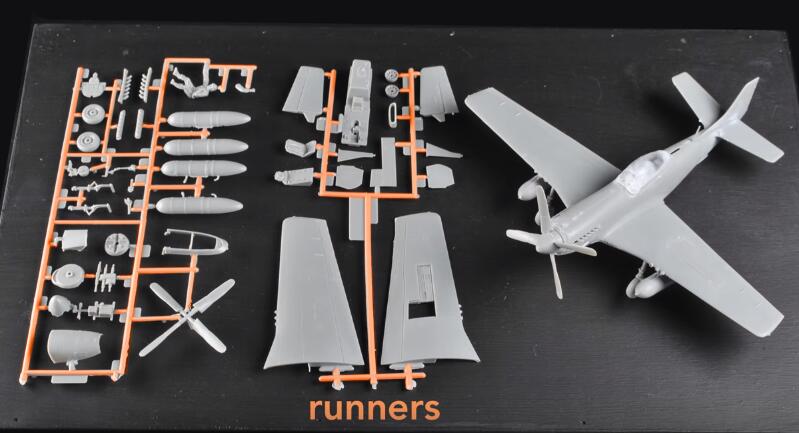
Whether the design of the gate system is reasonable will directly affect the appearance, internal quality, dimension precision and molding cycle of the molded plastic parts.
Concept and classification of feed system
The feed system of the mold is a section of the melt flowing passage from the nozzle of the injection molding machine to the cavity; it can be divided into two main types: cold runner system and hot runner system.
Ordinary the cold runner system is also divided into the side gate system and point gate system.
The gate system is composed of the main runner, sub-branch runner, the cold material well and the gate.
The hot runner system has no main runner and sub-branch runner. The melt passes through the manifold plate and the hot nozzle directly from the gate into the cavity.
Design principle of feed system
The design of feed system should follow the principles.
- (1) Ensure the appearance quality of the products.Any gate will leave traces on the surface of the product, thus it will affect the surface quality. In order to not affect the appearance of the product, design should try to set the gate in the invisible parts of the product. If it is impossible, the gate should be easily removed, and after the removal, the left traces should be the minimum.
- (2) Ensure the quality of the product.The style and quantity of the gate should be reasonable, which need ensure that the plastic melt quickly fill the cavity and the pressure and heat loss are reduced. The internal organization of products is fine.
The design of the gate system should prevent the defects of the products, like the shrinkage mark, short filling, flash, poor weld line, residual stress, deformation, uneven shrinkage, jetting, drooling, resin degradation and other defects.
The gate system should be able to smoothly guide the molten plastic to fill cavity in every corner, so that the gas can be discharged, avoiding the bubbles by trapped air.
The feed system should collect the melt material of the low temperature, prevent its entering the cavity and affect the quality of the products.
The gate and runner system are arranged balanced possibly. Melt plastic can be evenly filled in each cavity, so that the shrinkage rate of each cavity is uniform.
The good feed system design could improve the size accuracy of the plastic parts, and ensure the injection part to be interchangeable.
- (3) The minimum flow resistance.Flow path of the melt plastic should be as short as possible, turning should be reduced and the cross-sectional area of the runner should be reasonably. the appropriate cross-sectional area should be small. The reason is; increasing the small to the big is simple, but the contrary is hard;
The small runner reduces the proportion of waste material.;
The circular melt can fill the cavity in the shortest time to shorten the molding cycle and improve the productivity of the mold;
The less air in the feed system would reduce the venting burden of the plastic mold.
If The temperature and pressure loss of the melt in the flow channel are small, the molding quality of the product is easy to guarantee.
- (4)Not affect the automatic production.If the mold is designed for the automatic production, the feed system (runner and gate) should be able to fall off automatically.
Contents and steps of the feed system design
The design procedure and content are as follows:
- (1) The type of the gate system. According to the structure, shape and size of the product, they would decide its filling process, like the side gate system, the point gate system or the system without runner, and then determine the adoption of mold base.
- (2) The design of the gate.According to the structure, size and appearance of the product, determine the form, location, quantity and the size of the gate.
- (3) The dimensions and locations of the main runner
- (4) Design of branch runner.According to the structure, size and variety of the products, the shape and cross-section of the branch runner are determined.
- (5) Design of assistant runner.According to the follow-up process or the structure of the product, determine whether to design the assistant runner, and its Shape and size:
- (6) Design of cold material well.According to the length of the sub runner and the structure of the product, determine the location and size of the cold material well.